In today’s Oil and Gas industry, digital technologies play a crucial role. Indeed, the Middle East and North Africa (MENA) region invests heavily in digitalization and innovation of the sector to optimize energy production and boost sustainability.
At the forefront of the industry transformation are digital twins, virtual models that represent physical assets in real time. Leading oil companies in the region are actively implementing digital twins to enhance their operations. For instance, Saudi Aramco has developed the Sales Gas Monitoring, Analysis, and Reporting Tool (SMART), a digital twin of its Master Gas System pipeline network. This tool provides operational and maintenance insights, predicts survival times, and aids in load forecasting.
Similarly, the Abu Dhabi National Oil Company (ADNOC) has been recognized for its advancements in digital twin applications. The company received the Operational Digital Twin of the Year award for its Al Yasat Petroleum Intelligence and Wisdom Center, exemplifying operational excellence through innovative digital solutions.
Digital twins proved to drive efficiency, safety, and sustainability in the Oil and Gas sector. As investments in digital transformation continue to grow, the adoption of digital twin technology will play a pivotal role in shaping the future of energy production in the MENA region. In this article, we explore the key aspects and benefits of this breakthrough technology.
What are digital twins?
It all started with three-dimensional (3D) models of industrial assets that were (and still are) their digital replicas created using specialized software. 3D models are used to simulate various scenarios, analyze operational processes, and help solve a wide range of challenges. For example, during staff training, 3D models can simulate and demonstrate the operation of equipment safely, even in hazardous production environments.
With advancements in data collection and analysis, 3D models have evolved into digital twins, which are used in the Oil sector to manage production cycles. Digital twins not only provide comprehensive 3D representations of physical assets. They also include production processes, resource flows, personnel movement, and product tracking. Continuously updated with real-time data, digital twins offer an up-to-date view of asset conditions and operational performance and enhance predictive capabilities.
Currently, there are various terms (“digital oilfield”, “digital twin of the field”, “smart oilfield”, “platform”, etc.) circulating across the Oil and Gas industry. Most experts agree on the following distinctions:
- Geological model: Based on the initial state of the oil reservoir, this model estimates reserves and plans drilling operations. It is updated quarterly and interacts passively with the initial reservoir state.
- Simulation model: Built on top of the geological model, it dynamically analyzes fluid movement in the reservoir, guiding production volumes, drilling plans, and recovery strategies. It requires substantial computational resources and is updated quarterly, often by sector.
- Technological model: Focuses on surface infrastructure and pipelines, allowing for near-instant scenario analysis and results. For example, changing flow patterns can reduce network pressure and increase well output.
- Integrated model + Choke model: Combines hydrodynamic, technological, logistical, and economic elements, providing a holistic view of system performance for improved decision-making. The model is updated accordingly with changes in any of its components.
- Digital twin: A real-time virtual counterpart of physical assets or systems used for simulation, analysis, and optimization. At this stage, the digital twin is the most effective format for the virtual representation of an oilfield.
How a digital twin is developed and used
Developing a digital twin is a phased process.
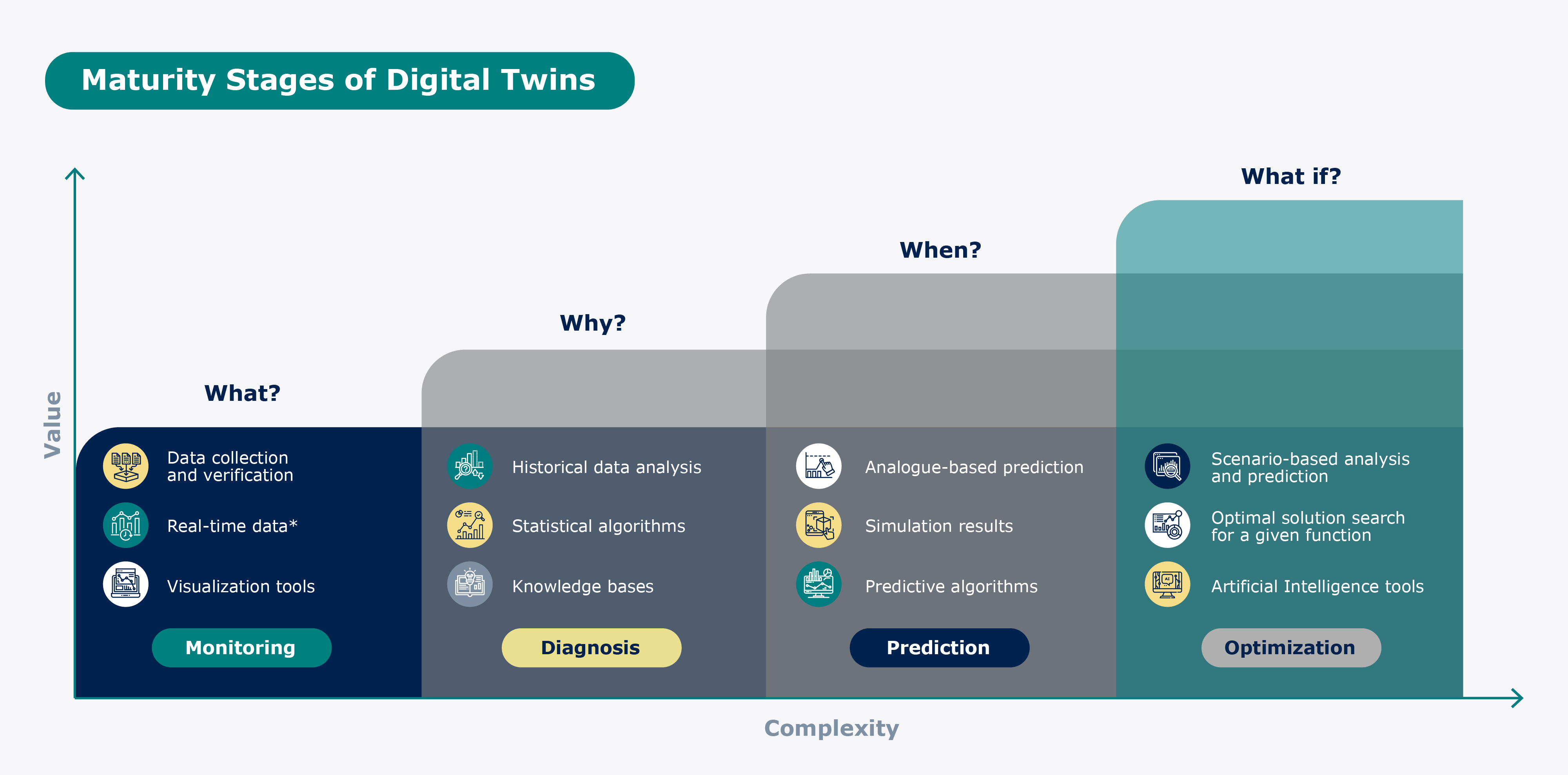
Stage one – Monitoring
The initial phase focuses on setting up the system and managing incoming data, including real-time inputs. This stage is feasible even for assets with a low level of technological maturity. Processing large volumes of data is complex and time-consuming, so it is crucial to prepare the data to extract valuable information for effective decision-making.
Stage two – Diagnosis
Based on accumulated data, statistical analysis is conducted to identify the causes of deviations and evaluate the effectiveness of corrective measures. This helps make more informed decisions and reduce the level of uncertainty.
Stage three – Prediction
At this stage, the digital twin is equipped with predictive analytics tools and forecasting models. These tools enable medium- and long-term action planning while accounting for changing factors.
Stage four – Optimization
This phase is characterized by the integration of the digital twin with geological and technical models and the automation of data updates. The use of artificial intelligence (AI) at this stage allows for the testing of various scenarios to find the optimal solution.
Over time, each digital twin acquires unique characteristics tailored to the enterprise’s specific needs, evolving from general functionality to customized solutions.
The benefits and drawbacks of digital twins
Digital twins offer significant advantages in optimizing operations and improving decision-making, but they also come with challenges that require careful management. Below is a breakdown of their key benefits and potential drawbacks to consider when implementing this transformative technology.
Benefits:
- Faster response times to equipment issues, reducing downtime and risk of accidents.
- Eliminates silos between departments, improving decision-making with continuous data streams and reduced human error.
- Enhanced data management positively impacts related processes.
- Helps detect anomalies and deviations in production performance, preventing overuse of resources like drilling fluid or methanol.
- Early warnings of potential issues such as wax or hydrate formation.
- Supports staff training through simulators, providing realistic, risk-free environments.
Drawbacks:
- Lack of standardization: Different approaches to digital twin development can hinder integration and compatibility.
- Data quality dependency: Digital twins rely on accurate and up-to-date data. Poor data quality can lead to misleading insights.
- Complexity and cost: Developing and maintaining digital twins requires significant expertise in areas like big data, modelling, and software engineering.
- Limited applicability: Digital twins may be less effective in environments with restricted data access or predictable behavior where simpler solutions suffice.
The future belongs to digital twins
The future of the Oil and Gas industry is closely tied to the adoption of digital twins.
These enhanced virtual models offer comprehensive functionality tailored to specific enterprise needs. For instance, a digital oilfield twin enables efficient management of production metrics, while an asset-level digital twin supports financial analysis, including cash flow, net present value (NPV), and profitability index (PI). By extending beyond technological aspects to include economic considerations, digital twins provide a holistic view of project performance.
As technological advancements continue, digital twins will remain an essential tool in the Oil and Gas sector, and their potential for delivering practical benefits will only grow over time.
How Axellect can help you
At Axellect, we believe that digital twins should enhance operational efficiency, not add complexity or unnecessary costs. Therefore, we aim to provide businesses with tailored, scalable, and cost-effective digital twin solutions that deliver real, measurable benefits.
Instead of a vendor-dependent approach, we focus on customized solutions that fully adapt to each client’s needs. By eliminating reliance on a single vendor, our digital twins seamlessly integrate with existing industrial platforms while reducing both initial setup and ongoing support costs. This makes digital twin technology more accessible, flexible, and future-ready for businesses.
Ready to unlock the full potential of digital twin technology? Contact Axellect today