Digitalization has drastically transformed industrial infrastructures and operations, and the metallurgy industry is no exception. Metal and mining companies around the world embark on digital transformation journeys to pursue a number of goals: become resilient and sustainable, enhance visibility, shorten time to market, switch to data-driven decision-making, improve sales and logistics operations, get an accurate prognosis and more.
The core element of any digital transformation is the digital platform that encompasses all the processes and operations of an enterprise. It naturally varies depending on the industry and the company’s needs. Here, we are going to dive into the perks of implementing a digital platform in the metallurgy industry, scrutinize its components, focus on the approaches that lead to success and pinpoint the benefits a metal factory may get from digitalization.
The state of business in the MENA region
But first, let’s have a look at the state of Metallurgy in the Middle East and Northern Africa (MENA) region.
The analytical company Fitch Solutions expects the MENA’s metals and mining industry to grow steadily in the coming decade, supported by significant government investment, particularly in the Gulf Cooperation Council (GCC). The main driver for this development is the government support for economic diversification away from hydrocarbons. While metals and mining may not be at the forefront of the various GCC diversification strategies, there is a growing trend toward investment in these sectors, especially in the UAE, Saudi Arabia, Bahrain, Oman and Qatar. This investment is expected to elevate production levels from their current relatively low status.
Additionally, Fitch Solutions underlines that the governments of the UAE and Saudi Arabia will invest heavily in producing low-carbon aluminium and steel over the coming years, pursuing their goals to achieve net-zero emissions by 2050. For example, one of the key players in the regional market, Emirates Steel Arkan, has already started developing low-carbon steel production in the UAE for domestic use and export.
Although the MENA’s share in global metal production is currently the smallest, the experts at Fitch Solutions forecast that it will double by 2032. However, the UAE already became the fifth-largest aluminium producer in the world in 2023.
Alongside this, MENA is booming with multiple digital transformation projects. Gartner forecasts that the region’s IT spending in 2024 will increase by 4% (compared to 2023) and will reach 183,814 million US dollars.
“IT spending in MENA is increasing because organizations, particularly in the Gulf Cooperation Council region, continue to focus on digitalizing their IT infrastructure,” said Miriam Burt, Managing VP Analyst at Gartner. “This is required to support regional governments’ push to implement their country visions for economic diversification, enhance public-private collaboration as well as bolster sustainability efforts towards net-zero targets.”
With these implications, it’s nearly inevitable that metallurgy enterprises in MENA should not only adopt digital solutions but reinvent themselves within large-scale digital transformation projects.
Digitalization and automation: what is the difference?
It’s the Industry X concept that is already forming and will continue to define heavy industry development. It’s that stage of evolution that relies heavily on Industry 4.0 solutions: Big Data, Visibility Tools, Artificial Intelligence (AI), Business Intelligence (BI), the Internet of Things (IoT), cloud computing and digital twins to drive a new-level efficiency, productivity, and innovation. Industry X represents a transformative leap beyond traditional industrial practices, integrating cyber-physical systems to create intelligent, interconnected operations.
This stage emphasizes the importance of predictive analytics, and this differentiates digitalization from mere automation that industrial enterprises have successfully implemented previously. While automation focuses on making existing processes more efficient without fundamentally changing them, digitalization is about leveraging digital technologies to transform business operations, models and strategies. Digitalization is far more than increasing efficiency and reducing costs; it creates new value.
Eventually, digitalization will have a broader impact. It reinvents how heavy industries operate and compete and how they respond to environmental and economic challenges, ensuring sustainability and resilience in the face of global changes.
Why does Metallurgy need digital transformation?
Digital transformation in Metallurgy is not just a trend but a necessity to stay competitive, innovative, and sustainable. Like many other industries, it can greatly benefit from integrating complex digital technologies that comprise digital platforms into its core processes.
Efficiency optimization.
By embracing digital platforms, metallurgical companies can automate and streamline nearly all operations, from raw material procurement to production and distribution. This leads to increased productivity and cost savings and ensures a faster time to market.
Data-driven auto-decisions.
The integration of digital platforms enables the collection and analysis of large amounts of data in real time, allowing for more informed, data-driven decision-making. This can improve everything, from operational efficiency to market analysis and strategic planning. Besides, real-time data and predictive analytics can help identify issues before they become costly problems.
Revamped supply chain management.
Digital platforms enhance supply chain visibility and collaboration among suppliers, manufacturers and customers. This results in better inventory management, reduced lead times and more responsive supply chain networks.
Innovation and product development.
Digital platforms facilitate research and development efforts by enabling simulations and modelling. This can accelerate innovation, reduce development costs and lead to the creation of new alloys and materials with improved properties.
Environmental compliance and sustainability.
Digital platforms can monitor and manage energy consumption and emissions, helping metallurgical companies comply with environmental regulations, reduce carbon footprint and move towards more sustainable practices.
Customer engagement and service.
Digital transformation creates new ways to interact with customers, providing platforms for custom orders, real-time tracking of production and delivery and enhanced customer service experiences.
Worker safety.
By incorporating IoT devices and sensors, digital platforms can monitor environmental conditions and ensure compliance with safety standards, reducing the risk of accidents and improving workplace safety. It goes even further: some operations and processes may be delegated to technologies to fulfill while a human stays responsible for the overall control.
Adoption and agility: Your way to building a digital platform
Digital transformation is all about adoption. It is a total reinvention of an industrial enterprise that embraces every process and operation a metallurgical company carries out on a daily basis. Inevitably, digital solutions should be implemented at each production level, making a complex digital platform and culminating in an Integrated Operations Centre where all the enterprise’s data are processed and transformed into actionable analytics. We at Axellect call it vertical digitalization.
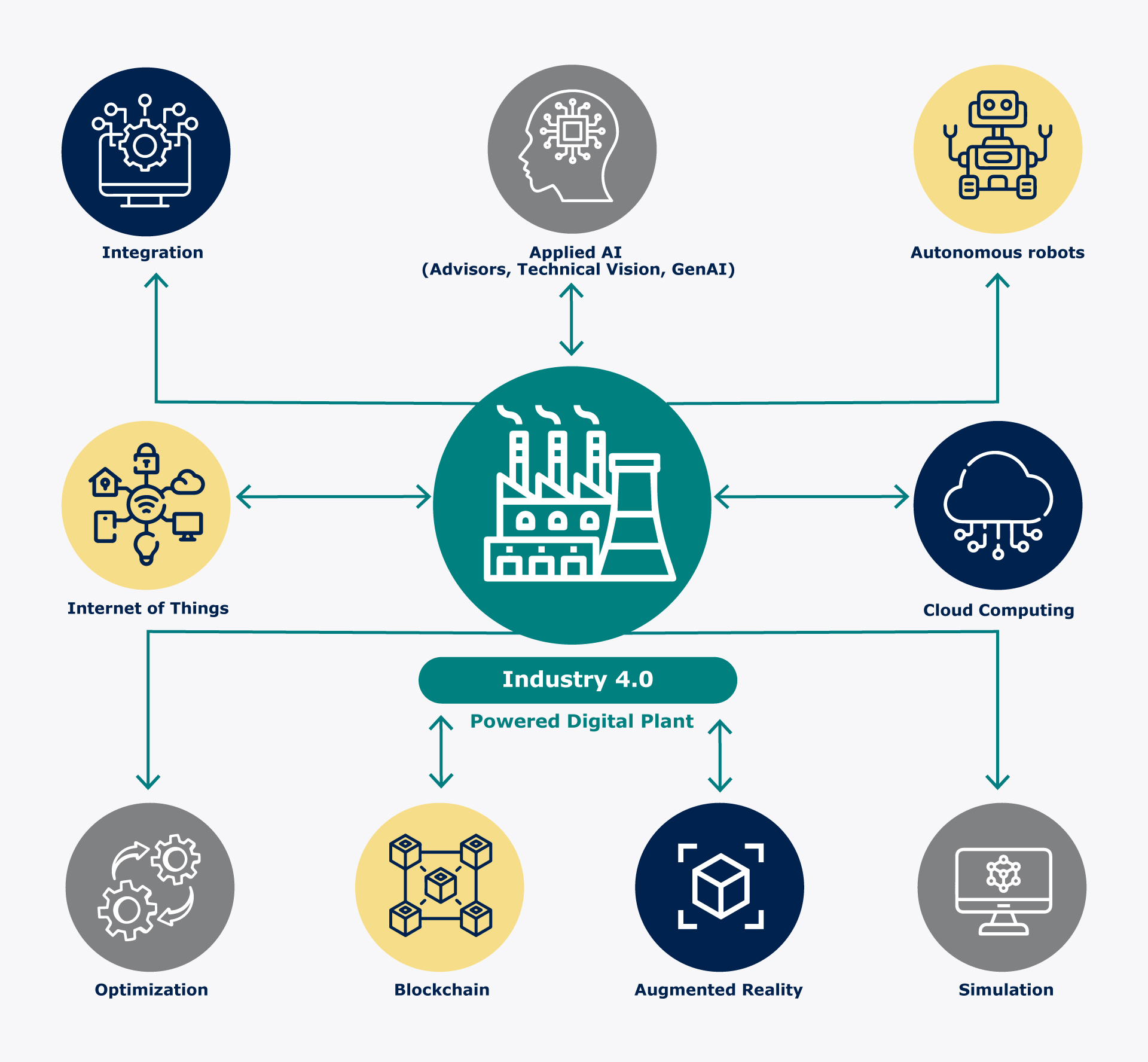
As simple as it sounds, the adoption approach does not have a universal set of technologies and solutions to implement as is in any given industrial company. With more than 1,000 projects in digital transformation fulfilled during the decades on the market, we at Axellect know that building a digital platform is always a from-scratch project.
To specifically address the unique challenges and goals of a metallurgical company, a digital platform needs to be assembled component by component, like a puzzle. Deploying digital solutions step by step allows addressing issues quickly and efficiently, prioritizing the most urgent or important tasks. And this is another cornerstone of a successful digital transformation: agility.
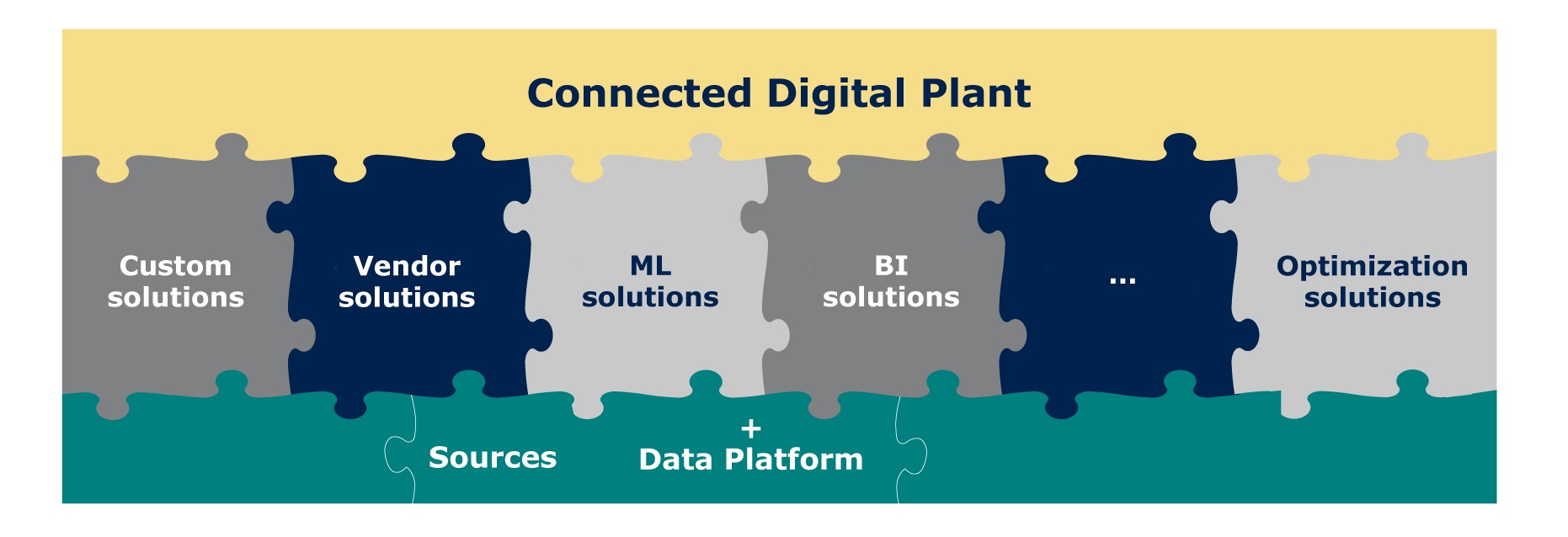
Agility, or the agile project management methodology, emphasizes adaptability and continuous improvement through iterative development. Unlike traditional, linear approaches, agile welcomes changes and deviations at any stage of the project lifecycle. It involves regular input and feedback from stakeholders and customers, ensuring the project remains aligned with the company’s needs and expectations. Agile’s core lies in its capacity to adapt swiftly to new insights and external changes, making it a dynamic and responsive approach to digital transformation projects.
For large heavy industries, it’s generally not that easy to switch to agility. Taking this into account, we at Axellect practice a so-called experimental approach to initiating a digital transformation project. It is precisely what we did for a metallurgical enterprise in Central Asia. In that project, we selected two factories within the large organization to start piloting various digital technologies to see their effects on everyday operations. The crucial goal of this pilot was to make the company accustomed to making decisions rapidly, trying various technologies and scenarios, adapting them upon the first results and being flexible. These capabilities are vital to succeed in digital transformation, which usually takes several years. So, by guiding a business through the agile approach before a huge and expensive digitalization project, we teach the company the core principles.
Results first
Digital transformation in Metallurgy is already happening. Digital technology fosters unprecedented efficiencies, shortens time to market, enhances customer and partner experiences and promotes sustainability. Companies that fail to embark on a digital transformation journey risk falling behind as their competitors advance.
What is needed to benefit from this global shift is a holistic digital framework. And from our experience, we know it starts with outlining the desired outcomes. It’s rather common practice for Axellect to evaluate the enterprise’s current infrastructure and processes, set final goals, elaborate a detailed strategy and develop a digital architecture. It’s a sort of reverse engineering: if you know where you should come to, you can successfully identify what solutions for particular functions, processes and systems you need to drive growth.
Interested to learn more? Talk to our experts.