A Manufacturing Execution System (MES) is an essential part of the IT landscape in any manufacturing enterprise. It acts as a bridge between Enterprise Resource Planning (ERP) systems, lower‑level Automation and Control Systems (ACS), and Advanced Planning and Scheduling (APS) systems.
An MES enables real‑time monitoring of nearly every aspect of production: the movement of raw materials and semi‑finished products, warehouse inventory, product output, equipment status, fleet management, etc. In other words, an MES system provides a complete overview of a plant’s current state, ensuring accurate tracking of production and movement of goods across all stages.
Implementing an MES is a resource‑intensive and high‑cost project. Its success largely depends on how well the system’s functional requirements are defined to match the company’s specific tasks and business needs.
In this article, we are sharing seven best practices that we have nailed through the years of our experience. We know these are working approaches to ensure comprehensive and high‑quality requirements gathering, which is the paramount first step towards a successful MES implementation.
Let’s start.
1. Define real business goals
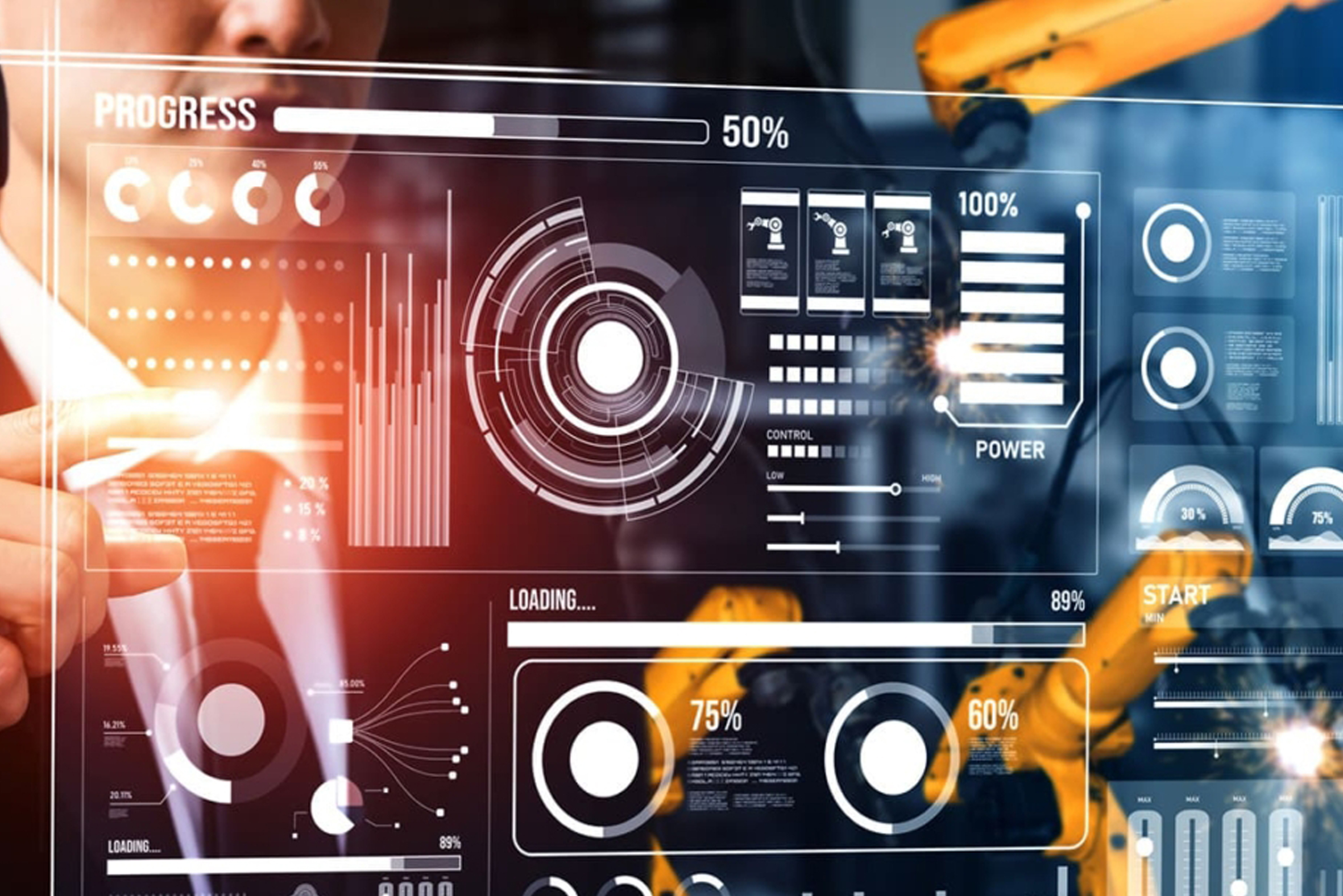
Our experience tells us that companies implement MES for different reasons. For some, the goal is boosting production efficiency, while for others, an MES is a foundation for digital transformation, enabling Industry X initiatives and advanced digital scenarios.
Therefore, it is crucial to define all input parameters and priorities at the early planning stage. These will shape the project plan and the list of functional and technical requirements.
The success criteria of the project also depend on the company’s objectives. A best practice is to define and document the business effects the company expects from an MES implementation before the project begins. Setting clear business goals encourages stakeholders to view MES as a tool for improving operational efficiency.
2. Get to know best practices
While interest in digital solutions is rapidly growing, many executives still lack a clear understanding of what MES is, why it is needed, and how to implement it.
Modern MES solutions differ significantly from the spreadsheet‑based approaches many enterprises are still using. Instead of flat tables, today’s MES platforms are advanced analytical tools that highlight critical insights and support decision‑making.
However, conveying these benefits through static documents and reports is ineffective. The best approach is to study real‑world MES use cases and industry best practices.
Many IT vendors now offer demo stands that allow companies to interact with a live MES system, explore real deployment scenarios, and test basic functions with anonymized data.
Key takeaway: MES implementation should not merely automate the existing status quo but introduce new management practices and operational improvements to manufacturing.
3. Engage employees in project discussions
A manufacturing plant may have thousands of employees, with hundreds using the MES system in some capacity. Each of these employees has unique expertise that should be considered.
For example, MES is often used for plan‑vs‑actual tracking, allowing dispatchers to compare current production performance against planned volumes. However, there are dozens of ways to visualize this data for operators.
Since manufacturing is a conservative industry, many employees remain silent until the last moment — and some may even resist the project altogether.
To increase the engagement and alignment of our customers’ employees, we at Axellect use design‑thinking workshops, either online or offline. These workshops allow people to voice their ideas and contribute to the project’s success.
And they provided valuable insights. In some sessions, we discovered that merely automating processes within a single department wasn’t enough; the enterprise needed cross‑functional collaboration. For example, MES had to be integrated with logistics functions for better shipment control or with finance departments to assess how production KPIs impact company finances.
4. Change operational models
Companies sometimes fail to achieve the full expected benefits from MES implementation. The main reason? MES requires organizational and process changes at the production level.
A best practice is to centralize production management by shifting control from individual workshops to a central dispatch center. This may also involve redefining dispatchers’ roles and responsibilities.
In such new organizational structures, dispatchers’ roles evolve from data collectors who manually log information to real‑time managers who track deviations, respond to incidents, and coordinate production activities. This shift creates new requirements for manufacturing management and planning systems, including MES.
5. Assess the current level of automation
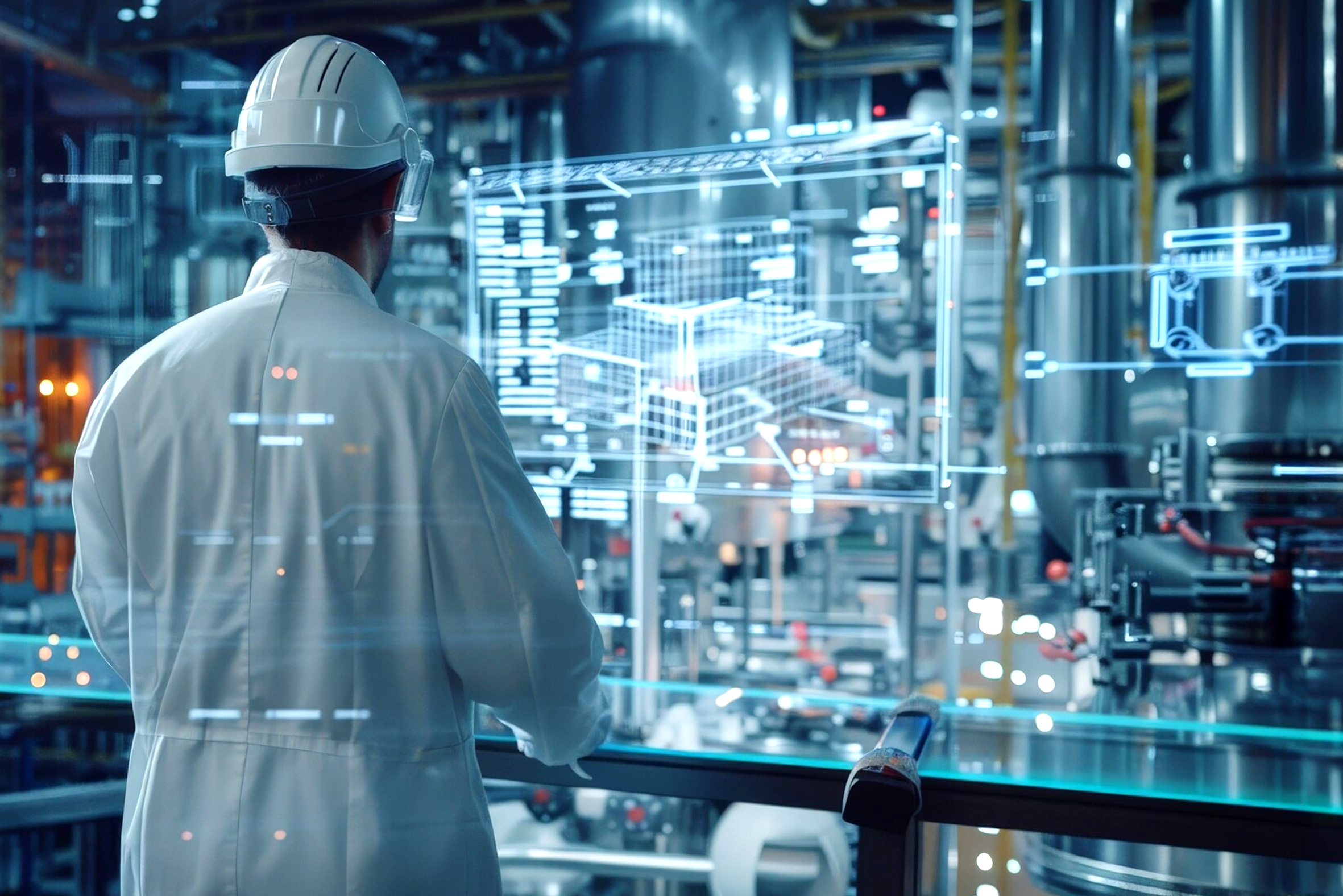
When defining MES requirements, it is crucial to evaluate the existing automation level, particularly the availability of industrial automation systems (ACS, SCADA, etc.).
Since most MES data comes from these lower‑level systems, the quality and speed of data entry directly affect MES performance. If employees enter data manually, the system’s accuracy will decrease, and workload will increase.
Therefore, pre‑MES implementation requirement gathering should include:
- Assessing automation maturity and coverage at the lower levels;
- Identifying integration needs with ERP, WMS, LIMS, and other systems.
Additionally, some functions overlap between MES and ERP. During requirement gathering, companies should decide which functions belong to MES and which should remain in ERP. This avoids redundancy and optimizes system efficiency.
6. Expand the project team
With rapidly changing IT infrastructure and security regulations, MES requirements must align with evolving compliance standards.
To ensure regulatory compliance and security, it is essential to include infrastructure and cybersecurity experts in the project team. These specialists help navigate evolving security standards, choose compliant IT products, and adapt quickly to regulatory changes.
7. Plan data migration thoughtfully
A smooth transition to a new MES requires careful data migration planning.
However, transferring all historical data at once is inefficient. It is often unstructured and requires enrichment before use.
We recommend the following step‑by‑step migration strategy:
- Identify the MES scenarios (e.g., plan‑vs‑actual tracking, quality control, analytics).
- Determine the specific tasks employees will perform in MES.
- Analyze which data objects are necessary to support these tasks.
- Prioritize critical datasets and migrate them incrementally.
This approach ensures that the most important data is transferred first while reducing unnecessary system complexity.
Final thoughts
Implementing an MES requires extensive preparation and should include:
- Comprehensive functional and technical requirement gathering;
- Stakeholder engagement and team alignment;
- Operational model adjustments.
With this preparation, MES implementation will be successful, budgets will be optimized, and project timelines will remain on track.
Additionally, proactive change management will minimize employee resistance, which is still one of the most common obstacles to automation in manufacturing companies.
Want to know more about migrating to a new MES or need expert guidance for the project?
Contact us today!